Knee pain is one of the most prevalent medical issues today, affecting nearly 25 percent of adults and steadily increasing. But what can be done about it? James Robinson ’26, chemical engineering, is working to help bring that percent down.
Robinson is spending his summer on Bucknell’s Lewisburg, Pennsylvania, campus working alongside Prof. Kenny Mineart to develop a shoe sole insert with varying levels of stiffness based on different polymer concentrations.
“We’re trying to get different gradients in a shoe sole with different stiffness to pronate the foot, thus helping to reduce pressure on the knee,” says Robinson. “The gel insert will easily conform to the contour of the foot and its materials are cost effective and recyclable.”
Robinson chose Bucknell because of the university’s prominent chemical engineering program and its beautiful campus. He was strong in chemistry and math in high school in Havre de Grace, Maryland, and that combination led him to chemical engineering. Robinson took a strong interest in materials science during an introductory course last fall and wanted to advance his knowledge about the subject this summer.
Midway through this summer, Robinson has created and tested gels with various concentrations of polymers, generally ranging from 10 percent to 40 percent. For each one he makes, he does compression and indentation testing to get quantitative data.
The gel made of 40 percent polymers needs approximately 155 Newtons to compress, which is likely the upper limit for the polymer concentration. Going higher will not allow the gel to compress enough to be effective. The 10 percent option starts to get bubbles in it when processed, which impacts the properties of the gel. That data and observation has helped Robinson focus his efforts to a limited concentration span.
To create the gels, Robinson combines a polymer powder with mineral oil and toluene, a colorless liquid that aids with dissolving the polymer. After mixing them together on a magnetic stir plate the mixture is placed on a rotary evaporator for up to five hours. Robinson then puts it into the oven to evaporate any residual toluene. After that, the gel can be molded into any shape desired.
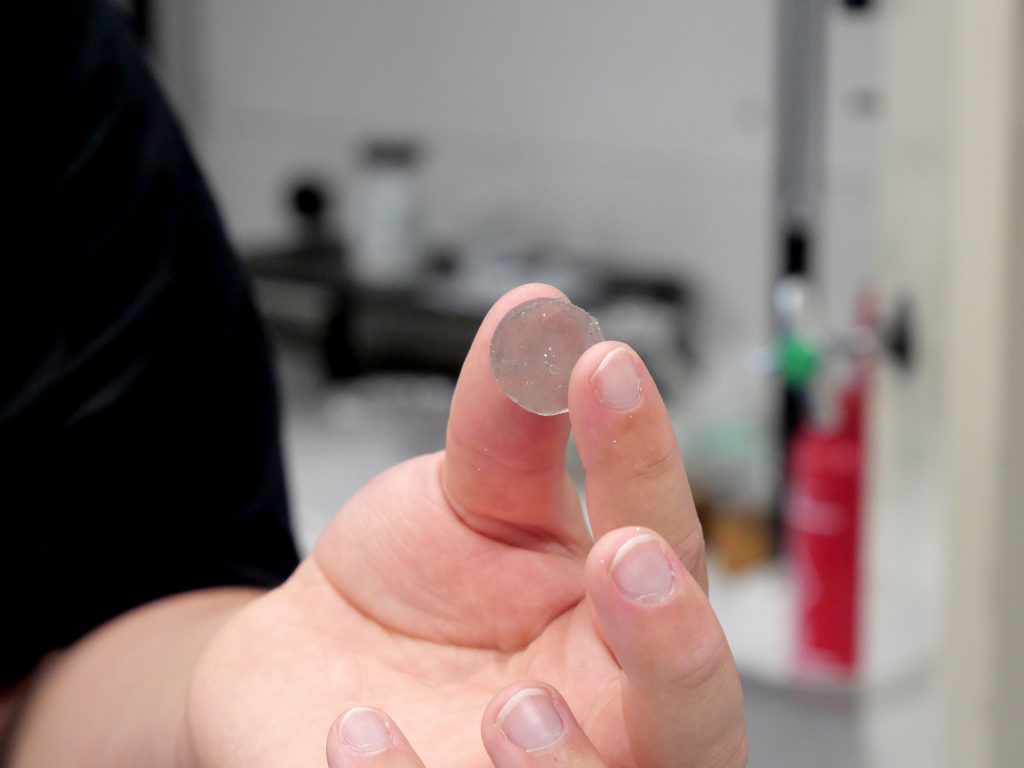
In a great example of interdisciplinary partnership, this project is in collaboration with Prof. Ben Wheatley in mechanical engineering, who specializes in biomechanics. As Robinson develops prototypes, Wheatley and his students will conduct analysis on how they pronate the foot and reduce the load on the knee.
“We are in the exploratory stages of making a gradient, but we do have quantitative data for gels at different percentages,” Robinson says. “We have a calibration curve comparing compression and indentation, and in the end we’ll compare quantitative values.”
An additional partnership has been formed between Robinson and his labmate Christian Owens ’26, chemical engineering, who is working with the concentration of dyes in gels and using spectroscopy to obtain quantitative absorbance values for gels of different dye concentrations. They plan to combine efforts and add a color gradient to the gel shoe soles that indicate the stiffness of each part of the sole.
Robinson’s ultimate goal for this summer is to develop a prototype and make it reproducible.
“Prof. Wheatley is working with a doctor at Geisinger and we have to keep progressing and gathering data before he will be ready to test it on patients,” says Robinson.
Many people experience knee pain and the gel inserts are meant for all audiences, not just those being actively cared for by a medical professional.
“When I was reading papers while preparing the proposal for this project, knee osteoarthritis was one of the common reasons for inserts. I also saw a lot about sports injury prevention,” Robinson says. “These are not meant for a particular demographic, though. They are to both help and prevent knee or joint pain.”
Thanks to Robinson’s work, you, a family member or a neighbor may soon be living a pain-free and more comfortable life.
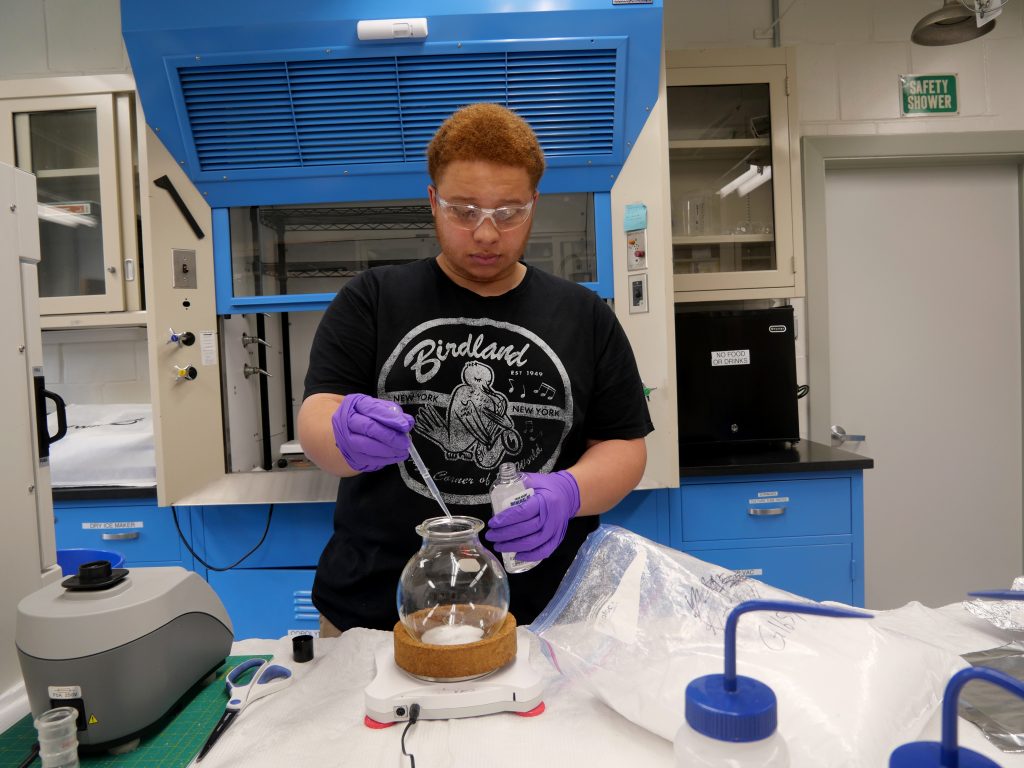
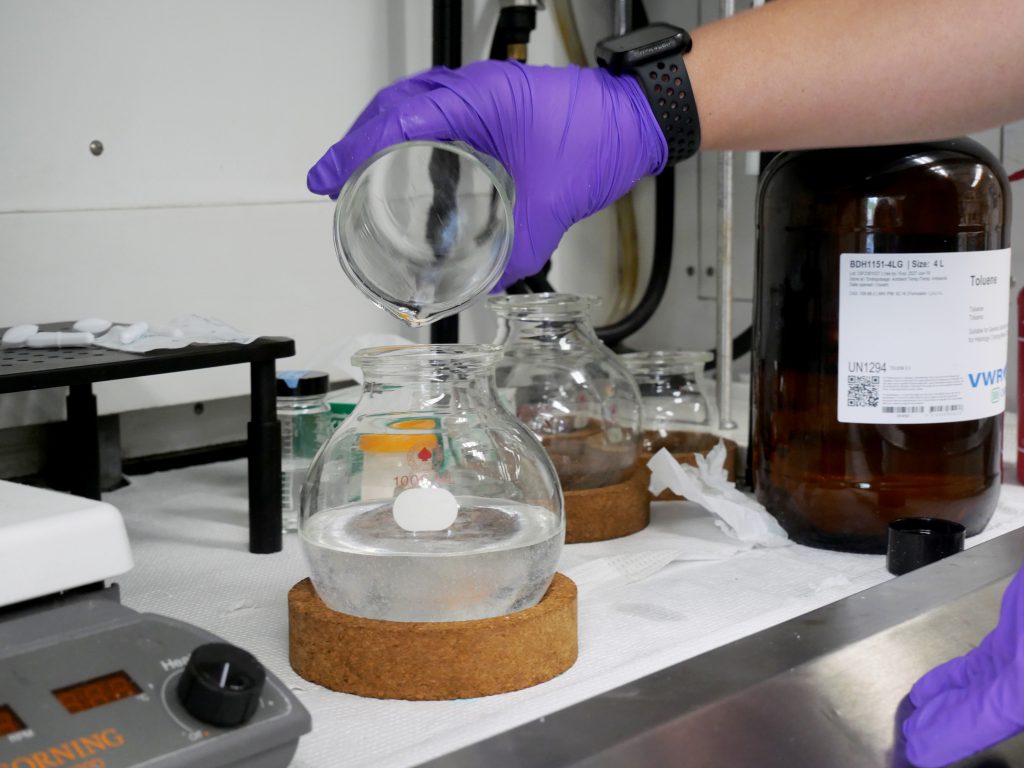